Project Story
微粒子技術を培いながら、
量子ドットのマーケットに新規参入
今や事業の柱に成長した量子ドット事業ですが、
T.Mさんが入社された頃のプロジェクトの状況を教えてください。
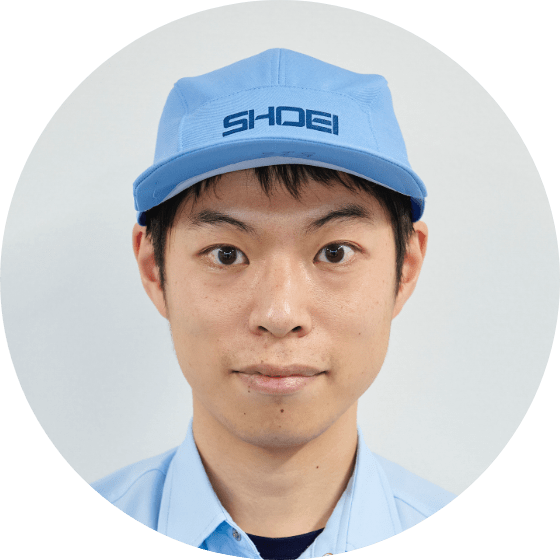
T.M: 私は大学院修了し、2013年に昭栄化学工業に入社しました。開発の一歩手前の段階を担当している開発企画部において募集があり、幅広い技術知識を生かし深められるという点に興味を持ち入社しました。
新規事業のプロジェクト自体は2011年から始まっていました。当社は電子材料の金属粉末のメーカーとして、トレンド的にはどんどん細かい粉末を作っていく必要がありました。そこで、このプロジェクトにおいては、当社のナノ領域の微粒子を作る技術を培いながら、ビジネスの芽を模索することになったのです。プロジェクトの活動の中で量子ドットの技術を持つアメリカのベンチャー企業と出会い、この企業のナノ粒子関連技術を買収しました。その後、この技術を足がかりとして、アメリカに研究所を作ったのが2013年ですね。
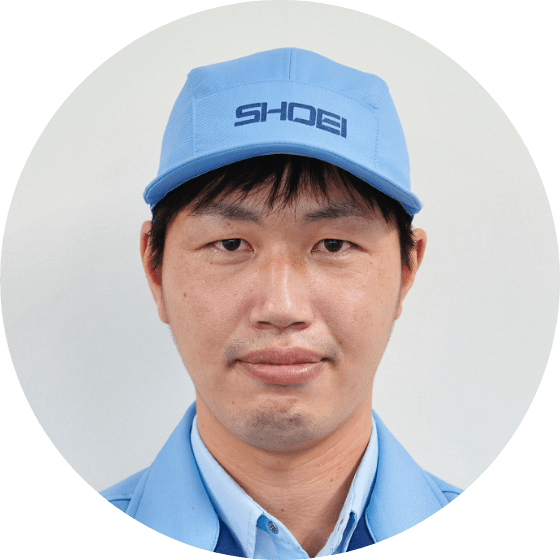
M.K: 2013年といえば、あるメーカーが量子ドット技術を搭載した液晶テレビを発表した年でもありますね。業界の注目が集まったのですが有害物質であるカドミウムが使用されていたことへの抵抗もあり、期待ほどは伸びなかったと聞いています。
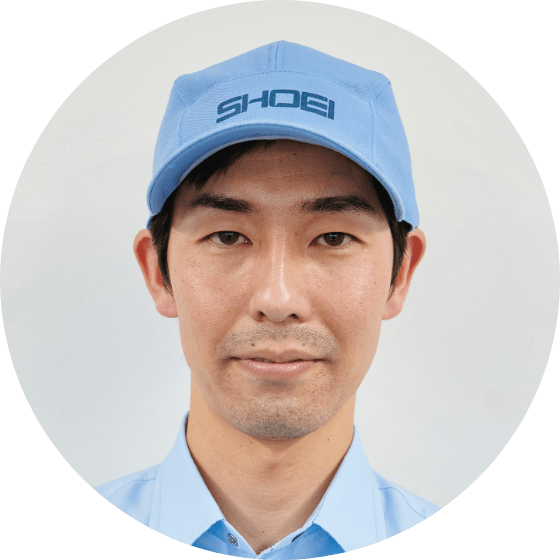
Y.H: その後、量子ドット技術では完全に後発の当社が日本で初めてカドミウムを使わない組成での量産に成功するわけですが、そのことは当時誰も想像できなかったでしょうね。
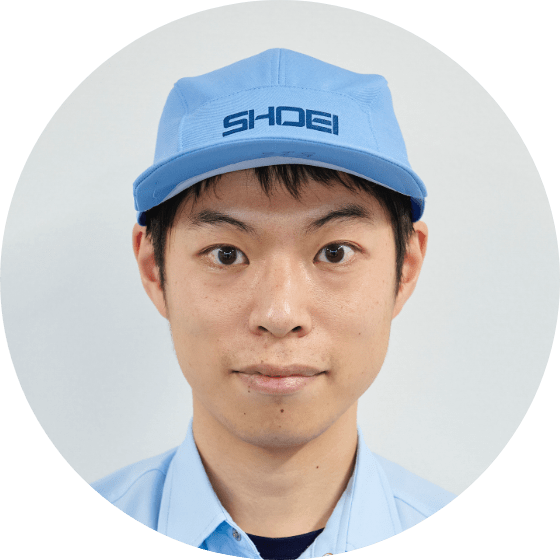
T.M:
私が入社した頃の当社はアメリカの情報収集に力を入れていて、私は入社わずか2週間目でプロジェクトリーダーと一緒にシリコンバレーに出張に行き、ベンチャー企業を訪ねて彼らの技術を評価していました。粒子合成とそれをどんなアプリケーションに用いるかを中心に調査し、帰国後に当社の技術と組み合わせて何ができるかをずっと考えていました。
実は、アメリカでは1993年頃からナノ技術に取り組まれていて、ベンチャー企業も多かったので、当社はこれに対しては20年ほど遅れてのスタートになります。そのため、追いつくことはかなり大変だと覚悟していました。
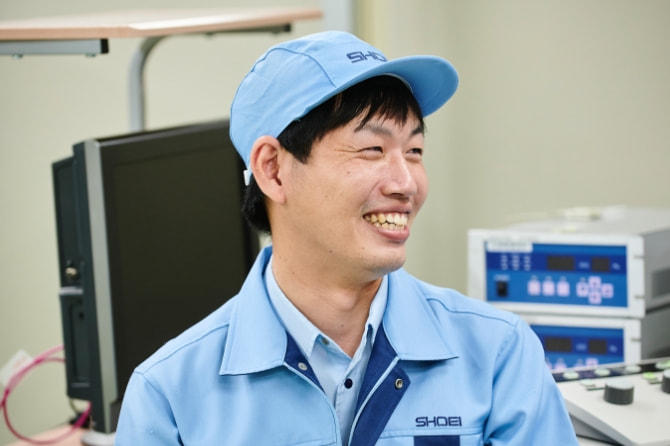
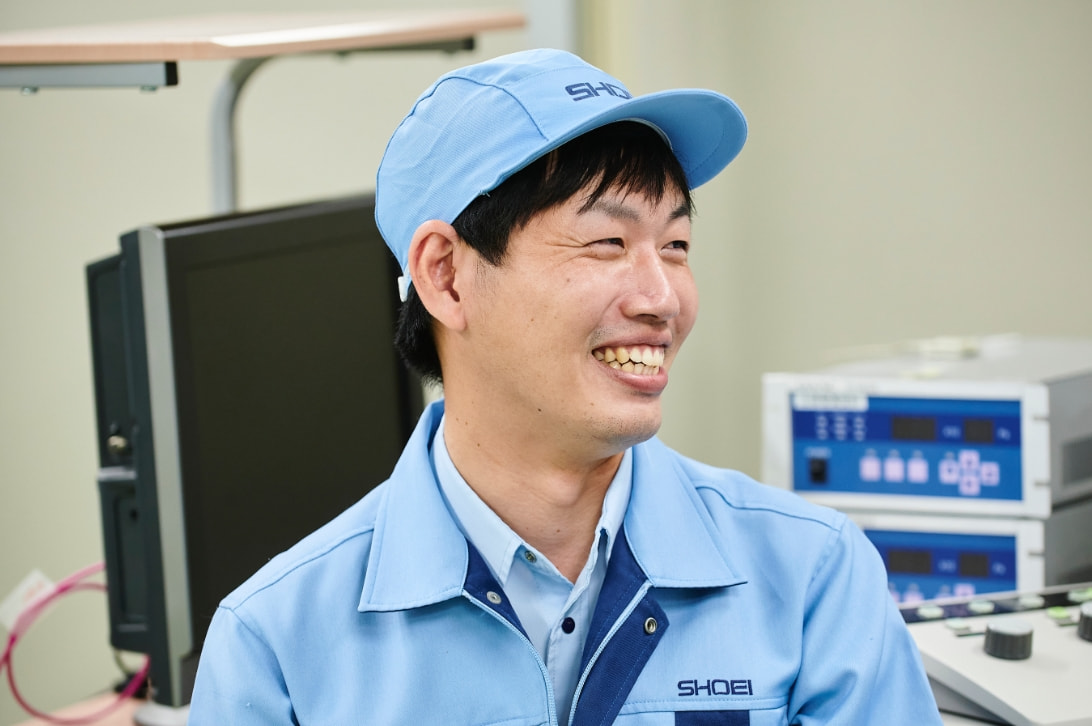
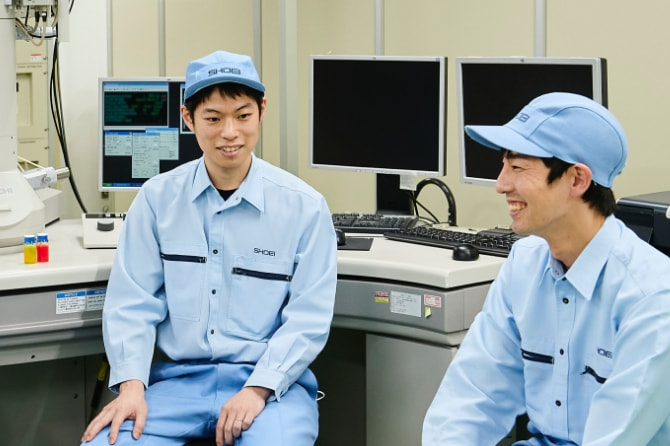
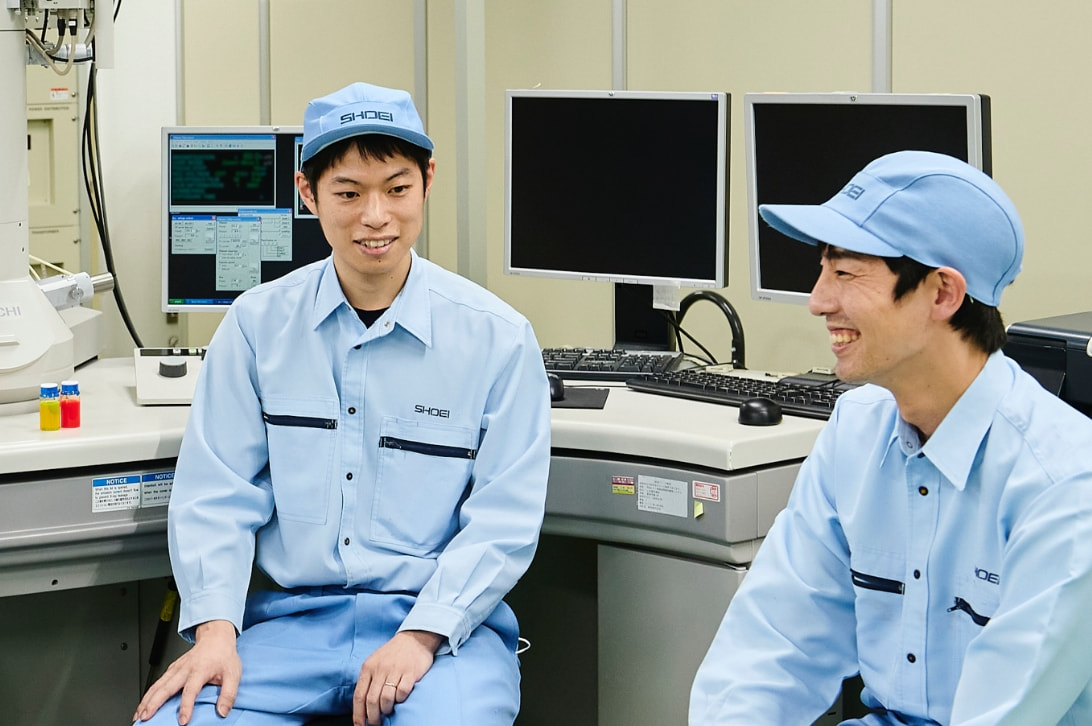
世界の先進企業と渡り合えるレベルに
大きな一歩で、事業化に確かな手ごたえ
量子ドットでは後発だった昭栄化学工業が独自の技術で戦い、
トップクラスと肩を並べました。そのお話をお聞かせください。
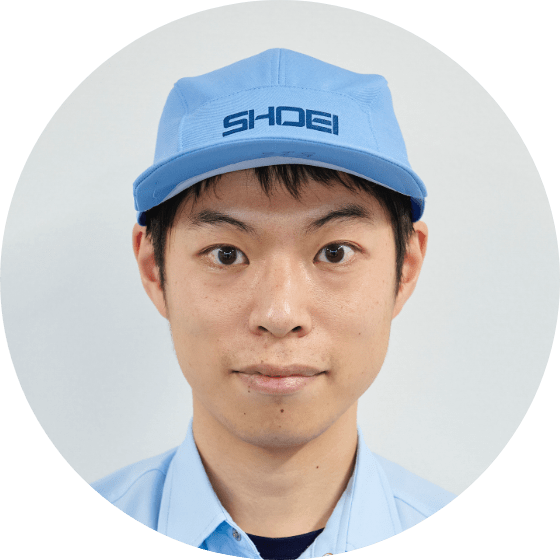
T.M: 当社と競合他社との特性比較において、最も先行しているであろう企業の特性値を超えたことは、QD事業にとって大きなステップになりました。私は「半導体ナノ粒子の製造」に着目し、2014年にR&Dチーム研究員としてアメリカの子会社へ出向となり、3年間本格的な研究に取り組むことになりました。現状、QD事業は順調に進んでいますが、渡米直後は他社から数年以上遅れていることを実感し、後発のつらさを味わいました。
出向中、私はある技術的な問題を抱えていたのですが解決の糸口がみつからず、実験中だけでなく、空き時間も考え続けていました。実験回数は2,000回を軽く超えていたと思います。そんなとき、ある薬品を使うアイデアがわいてきたんです。それを試したところ、劇的に変化しました。この瞬間、体が震えました。理系の神様がヒントをくれたんだと思いました。これで先行企業と戦えると確かな手応えを得ました。「負けたくない、何としてでもいいものを作る」そう自分自身で思い続け、研究に向き合ってきました。いま考えると、戦っていたのは競合企業ではなく、自分自身とだったのだと思います。
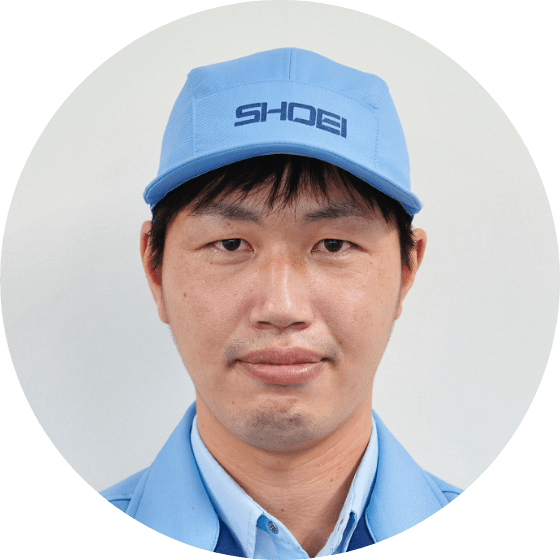
M.K: 実験レベルでの特性は、先行するトップクラスの企業と肩を並べましたが、ここがスタート地点。ここからビジネスとして成り立たせるには乗り越えなくてはならないハードルが数えきれないほど待ち構えていました。
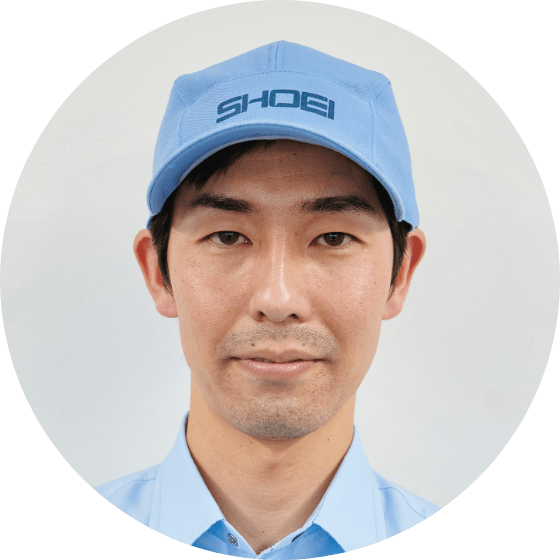
Y.H: 良い特性のモノができるのと、製品として売っていくのは違う。製品として販売するにはただ実験をして特性を出すのとはまた違った視点が必要ですよね。
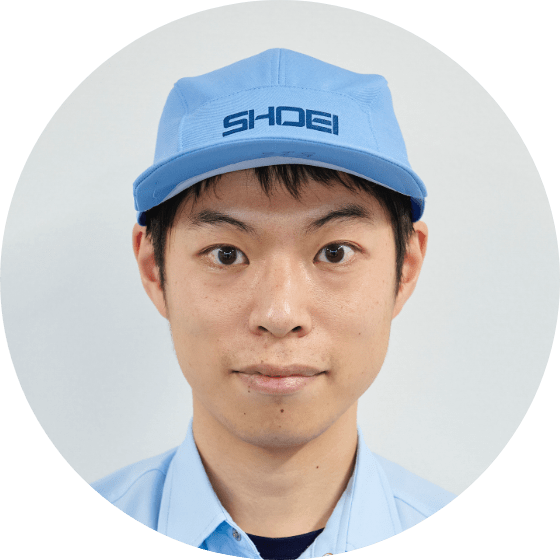
T.M: 開発当初は、ナノ粒子なのでそれほど量は作れないという予想をしていましたが、ディスプレイというマーケットにおいては相当のボリュームの生産量が必要になり、かつ、それを安定供給できなければなりません。鳥栖に研究所を立ち上げるタイミングでチームに有機化学の専門家がいなかったため、第一人者であるM.Kさんが抜擢されました。
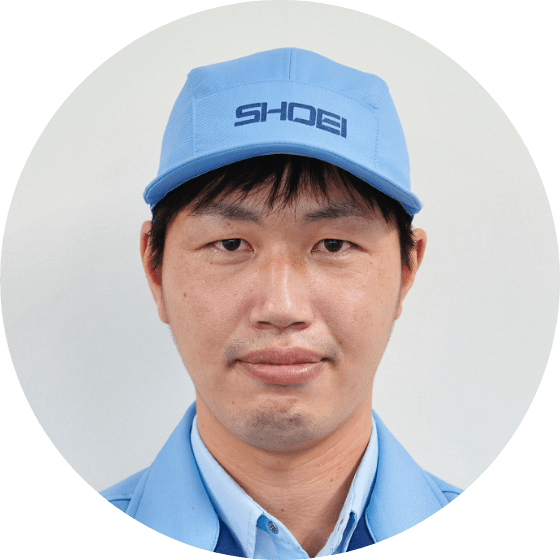
M.K: 量子ドットは半導体ではありますが、リガンドという有機物の分散剤がたくさん付いているため有機化学の知識が必要になります。配属された当時は、「自分が研究所で一番詳しくなるんだ!」という思いを抱きながら、研究所の立ち上げに取り組んでいました。
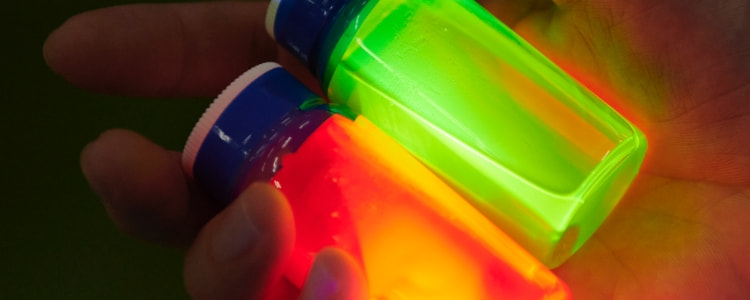
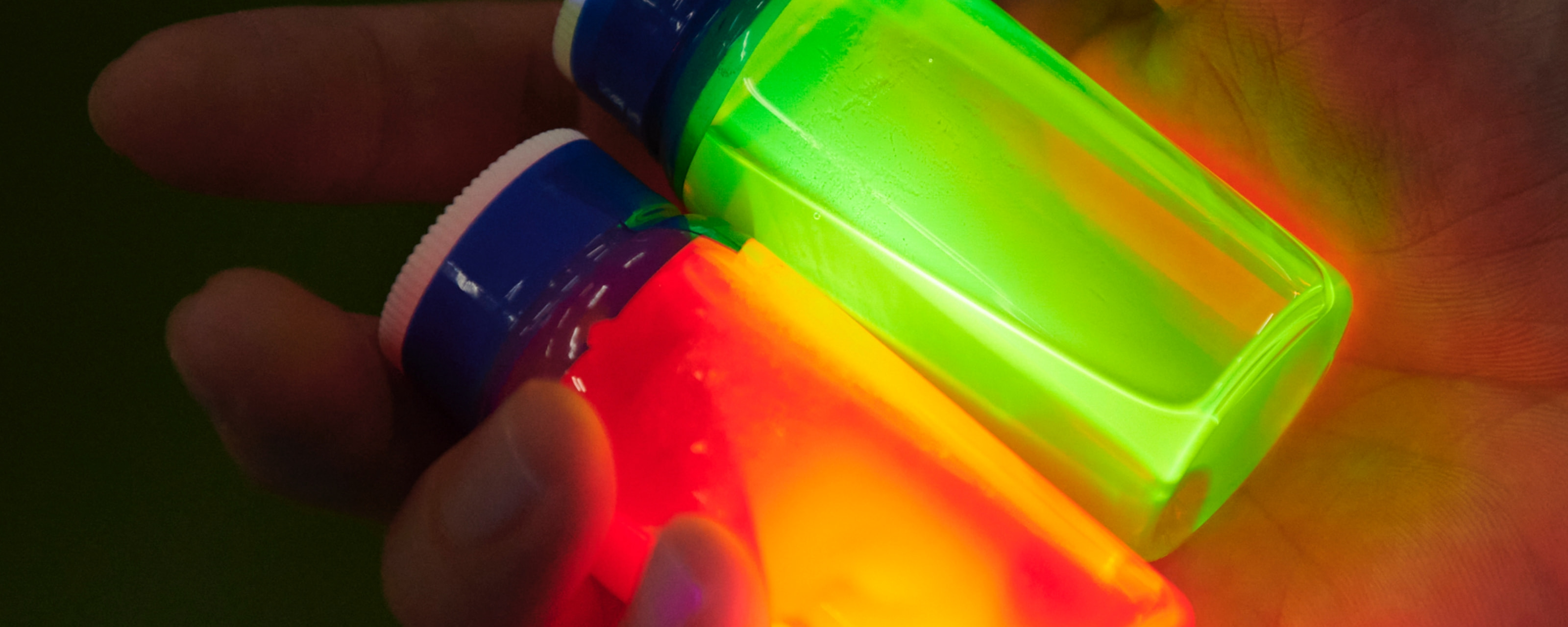
「量子ドットといえば昭栄化学工業」
そんな未来に向かって、新たなフェーズへ
研究室から工場へ。
量子ドットの量産化で苦労された点や今後取り組みたいことなどを教えてください。
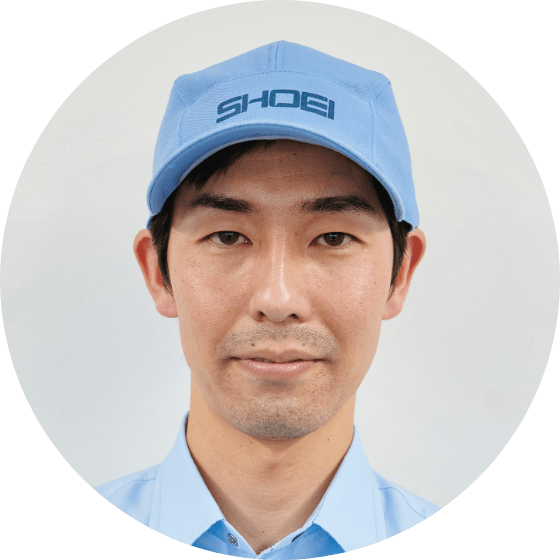
Y.H: 私がQD事業部に異動した2020年は、工場が完成間近で、本格的な稼働開始の直前でした。プロセスの90%程度はすでに決まっていましたので、私は最後の部分だけ関わるのだと思っていましたが、それは簡単なことではありませんでした。プロセスの最終仕上げを担当し、製造プロセスを完成させることの大変さを痛感しました。
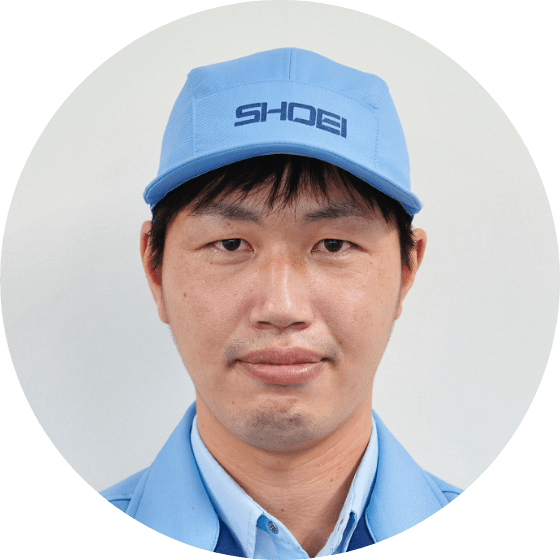
M.K: それまでフラスコで作っていたものを1,000倍、1万倍とスケールアップしていくと、少量試作の際は起きなかった不具合が起こることもあり、条件を調整する必要がどうしても出てきますね。そこが大変難しいところのひとつです。そこをなんとか乗り越えて、初出荷の日を迎えた日は本当にうれしくて、初出荷製品を囲んでみんなで写真を撮りました。元々、鳥栖で量子ドットの開発が始まった頃は10人ほどだった関係者が、このときには30人近くになっていました。「こんなにたくさんの人に支えられて、ここまで来たんだ」と感慨深かったです。
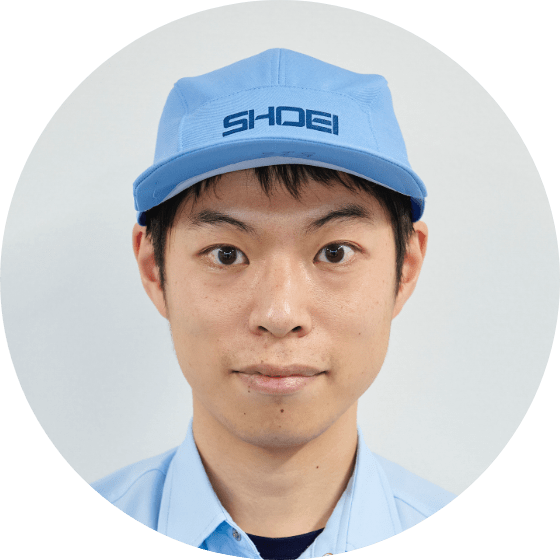
T.M: 「よくここまで来たな」と思いましたね。私は輪の中というより、少し後ろに下がって全体を見るような立場でしたが。プロジェクトの当初の目的は、今まで当社の持っていた技術では達成できない細かさの粒子を作ることでしたので、今後はこの技術を、量子ドットに限らず体系化した技術として、ナノ粒子の製造方法としてまとめ、成熟させていくことに取り組みたいと思っています。
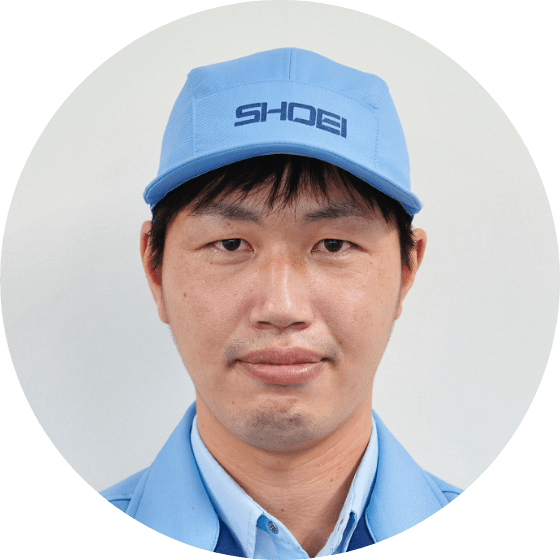
M.K: 工場でいろいろな装置を動かしていますが、装置の持っているポテンシャルを最大限まで引き出したいです。まだまだ引き出せる余地があるので、今はその調整に取り組み始めたところです。装置の能力を最大限発揮して、さらに高品質で競争力ある製品を作っていきたいです。
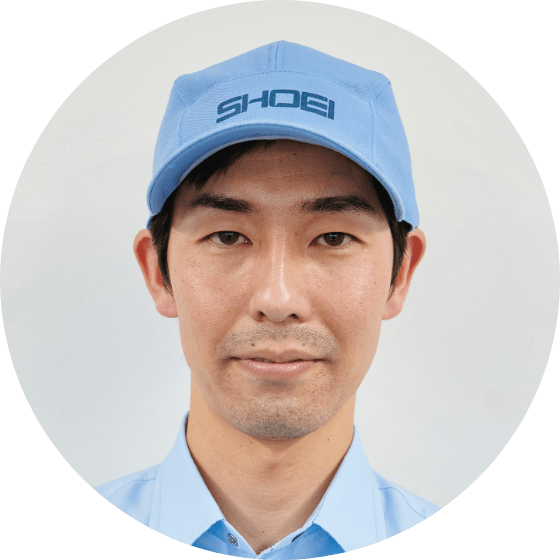
Y.H: 世界的企業やアメリカのベンチャー企業と比べても製造コストを抑え、安定供給できるのが当社の強みです。これからは製造実績を積み重ねて、ナノ粒子製造の生産技術力をもっと磨いていきたいですね。長期的な目標としてはたくさんのディスプレイに搭載され「量子ドットといえば昭栄化学工業」とお客様や関係者から思われる存在を目指したいです。
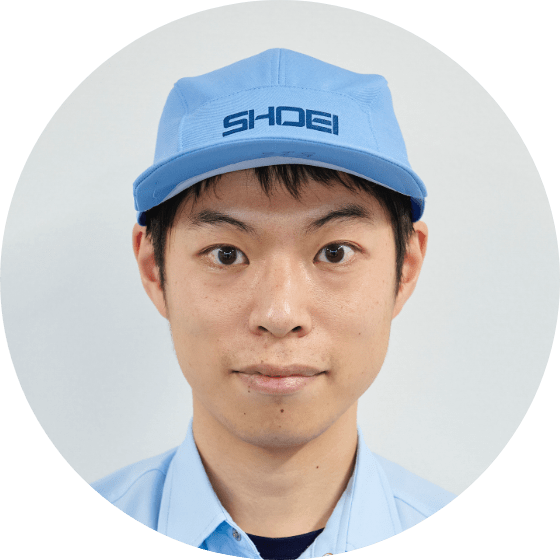
T.M: 量子ドットは反響が大きく、これまでお付き合いのなかった業界の方とお会いすることも増えています。そこから新しい用途につながっていく可能性が高い。QD事業部の挑戦はまだ始まったばかり。昭栄化学工業の新しい歴史を作るつもりで、これからも前に進んでいきたいです。
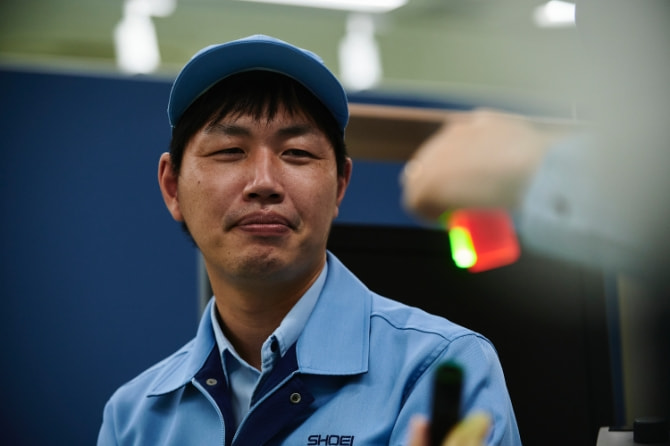
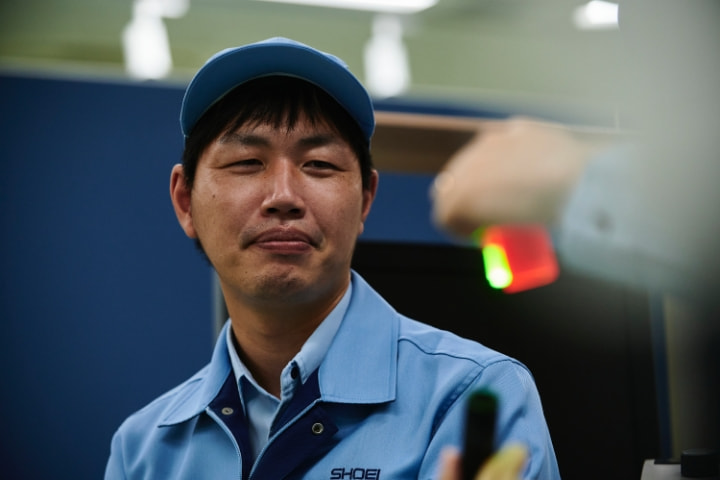
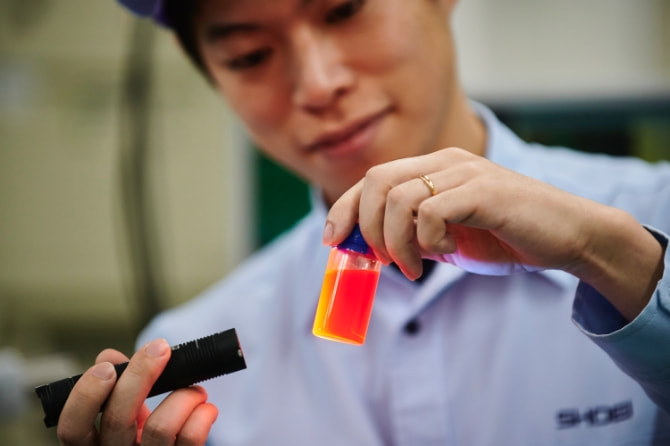
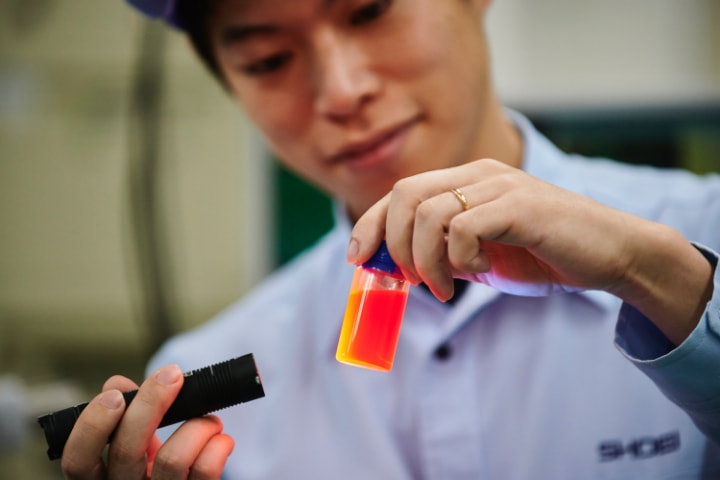
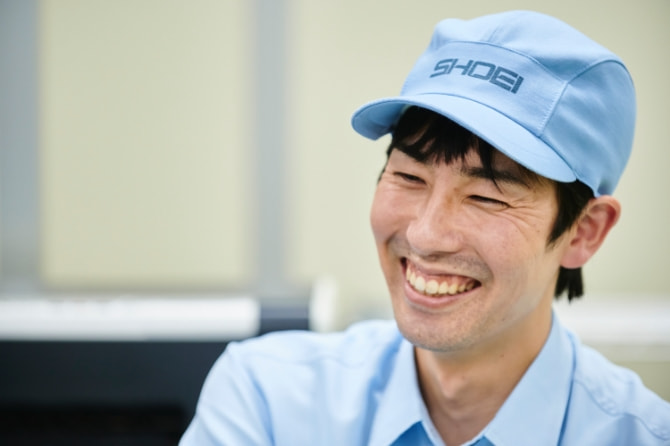
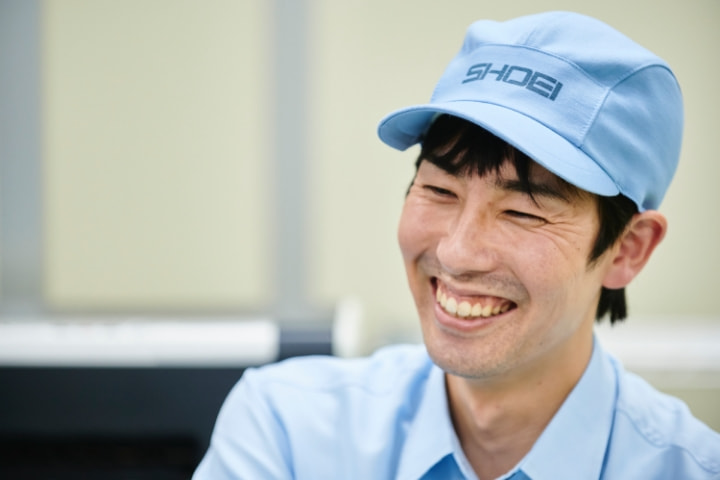
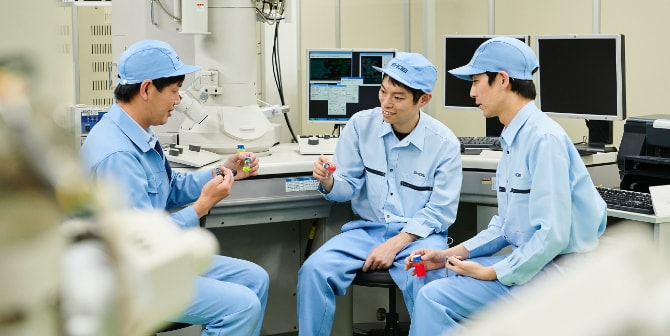
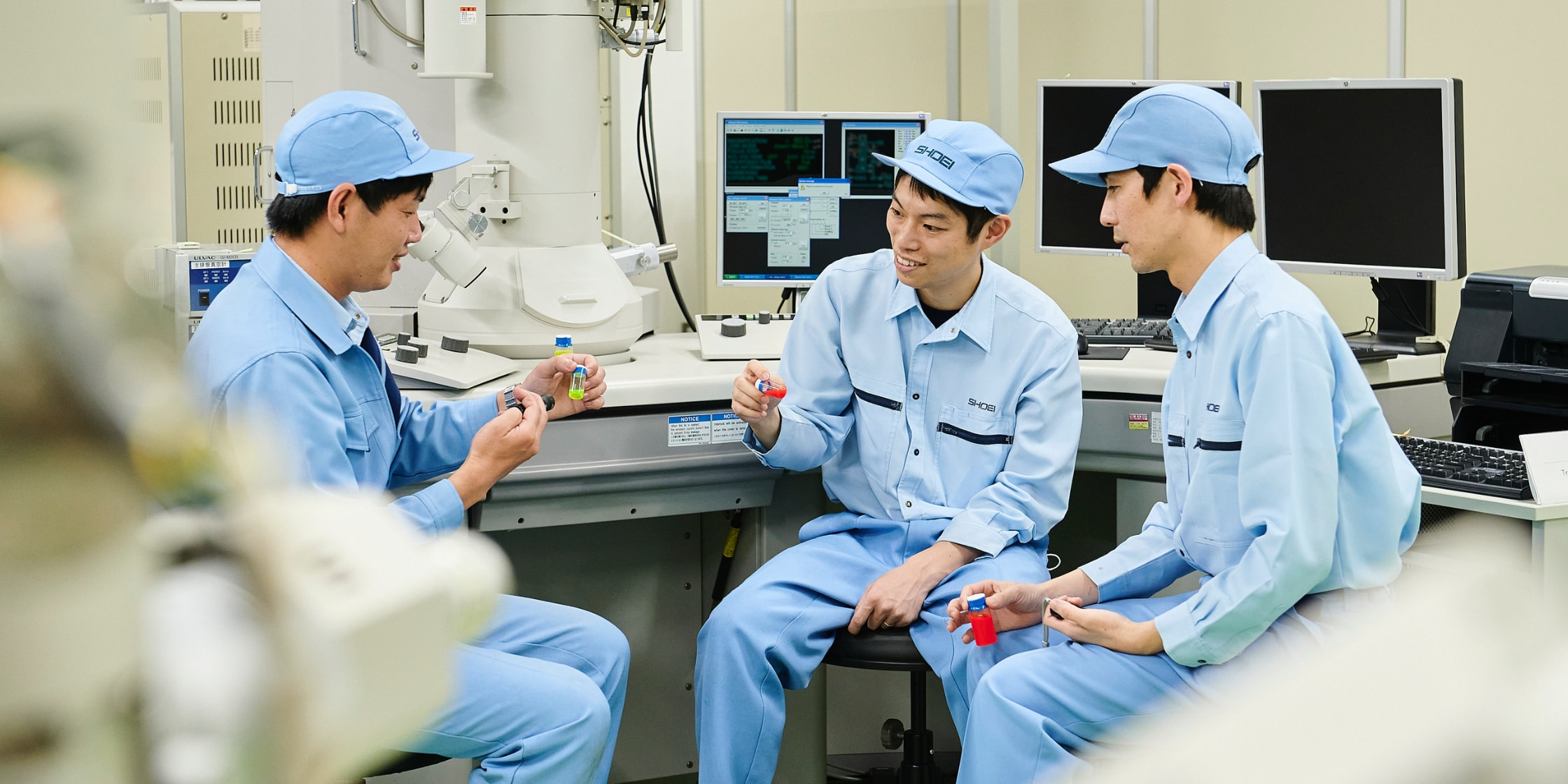